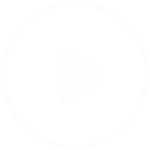
Challenges in the apparel industry
Clothing companies face many challenges such as consumer demand, production management, operating costs, and employees.
-
Practitioners
Big gap in the ability of employees
Practitioners
Big gap in the ability of employees
The clothing supply chain is all about large-scale production, slow response, long cycle, high work-in-progress and inventory rates, and high overall costs. -
Production Management
Management efficiency needs to be improved
Production Management
Management efficiency needs to be improved
The clothing supply chain is all about large-scale production, slow response, long cycle, high work-in-progress and inventory rates, and high overall costs.
-
Business Costs
Business costs remain high
Business Costs
Business costs remain high
The clothing supply chain is all about large-scale production, slow response, long cycle, high work-in-progress and inventory rates, and high overall costs.
-
Consumer Demand
Industrial reform is imminent
Consumer Demand
Industrial reform is imminent
The clothing supply chain is all about large-scale production, slow response, long cycle, high work-in-progress and inventory rates, and high overall costs.
The infrastructure construction of the clothing factory is backward, the management is fragmented, there are data silos, and the progress of intelligence is slow.
-
Base Installation
-
Base Installation
-
Base Installation
Intelligent Application Common Problems Faced by Garment Factories with 200 People or Less - Automation and Lean Transformation
Intelligent Application Common Problems Faced by Garment Factories with 200 People or Less - Automation and Lean Transformation
Factory without planning:
The factory area is small, large-scale automated equipment cannot be accommodated, the floor is too low for hanging logistics lines, and the space utilization rate is low. The layout of the five major modules is unreasonable. Poor connectivity, wasting transportation time.
Less automation equipment:
There are few automated sewing equipment, and quality can only be ensured by skilled workers. It is difficult to recruit technicians, and the time and personnel costs are high. There is automated equipment, but the layout and quantity of the equipment are unreasonable, and production efficiency has not improved;
The process layout is unreasonable:
There is no assembly line formed according to the clothing style process, and secondary backflow is serious; there are many and far off-line processes, and the transportation cost is high;
5S management chaos:
Various tools are not arranged in categories, have no labels, and cannot be managed visually. The equipment is not cleaned after the work is completed, which can easily cause equipment damage and delay the construction period.
Intelligent Application Common Problems Faced by Garment Factories with 200 People or Less - Automation and Lean Transformation
Intelligent Application Common Problems Faced by Garment Factories with 200 People or Less - Automation and Lean Transformation
Factory without planning:
The factory area is small, large-scale automated equipment cannot be accommodated, the floor is too low for hanging logistics lines, and the space utilization rate is low. The layout of the five major modules is unreasonable. Poor connectivity, wasting transportation time.
Less automation equipment:
There are few automated sewing equipment, and quality can only be ensured by skilled workers. It is difficult to recruit technicians, and the time and personnel costs are high. There is automated equipment, but the layout and quantity of the equipment are unreasonable, and production efficiency has not improved;
The process layout is unreasonable:
There is no assembly line formed according to the clothing style process, and secondary backflow is serious; there are many and far off-line processes, and the transportation cost is high;
5S management chaos:
Various tools are not arranged in categories, have no labels, and cannot be managed visually. The equipment is not cleaned after the work is completed, which can easily cause equipment damage and delay the construction period.
The infrastructure construction of the clothing factory is backward, the management is fragmented, there are data silos, and the progress of intelligence is slow.
Intelligent Application Common Problems Faced by Garment Factories with 200 People or Less - Automation and Lean Transformation
Factory without planning:
The factory area is small, large-scale automated equipment cannot be accommodated, the floor is too low for hanging logistics lines, and the space utilization rate is low. The layout of the five major modules is unreasonable. Poor connectivity, wasting transportation time.
Less automation equipment:
There are few automated sewing equipment, and quality can only be ensured by skilled workers. It is difficult to recruit technicians, and the time and personnel costs are high. There is automated equipment, but the layout and quantity of the equipment are unreasonable, and production efficiency has not improved;
The process layout is unreasonable:
There is no assembly line formed according to the clothing style process, and secondary backflow is serious; there are many and far off-line processes, and the transportation cost is high;
5S management chaos:
Various tools are not arranged in categories, have no labels, and cannot be managed visually. The equipment is not cleaned after the work is completed, which can easily cause equipment damage and delay the construction period.
What solution can Jack offer?
-
Intellectualization
Build a cloud database,connect and drive various systems, and build business processes with lOT, Internet and cloud computing technologies to achieve full and efficient personalized delivery.
-
Digitization
Develop a digital platform, build a system,CA D system,MES system,WMS system,SSCM system and APS system to improve design efficiency and management level.
-
Automation
Complete sets of automated hardware equipment,one-stop supply from before,during and after sewing.
-
Lean
Provide research and rectification reports,Such as factory layout,process adiustment, production line analysis,standardized operation and efficiency analysis to guide factories to enter lean production.
Jack intelligent complete solution
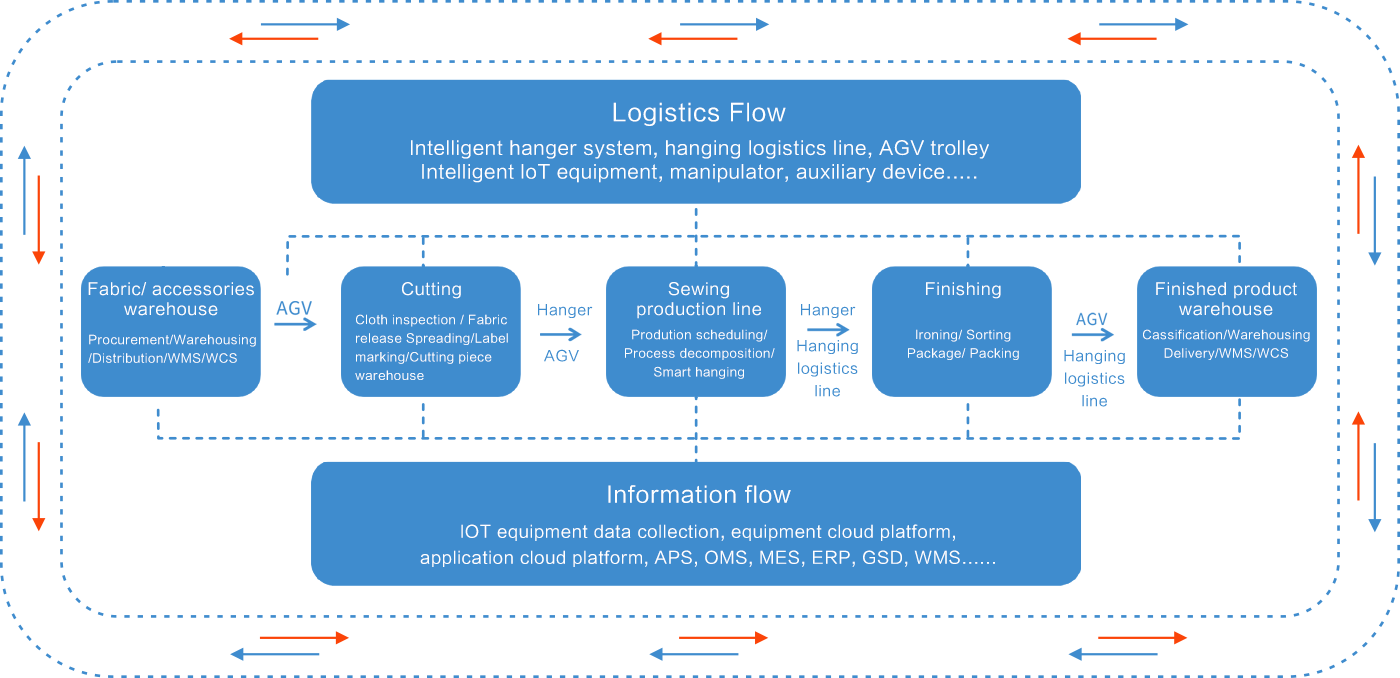
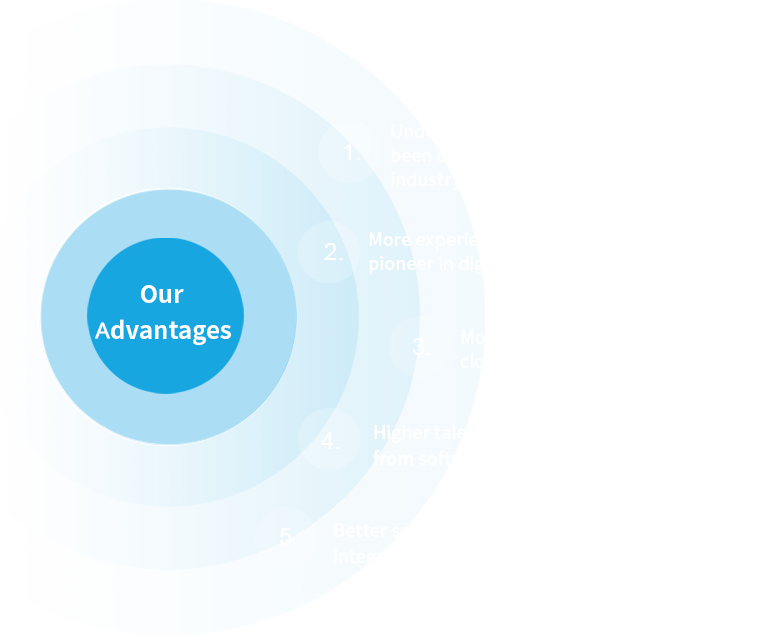